|
Delinda
VanneBrightyn
Fine Art Sculpture in
Glass and Bronze
|
HOME BIO PROCESS SCULPTURE WALL WORKS ARCHITECTURAL UPCOMING SHOWS GALLERIES |
|
- THE ARTIST'S
PROCESS
-
-
- "I see, I
dream
light, texture, beauty, & form
- dancing through
space.
It presses me to exist.
I attempt to oblige."
- Delinda VanneBrightyn,
2003
|
Inner Page Navigation:
- The Very Beginning
- The First
Mold-Making Process
- The Kiln-Formed
Glass Process | The
Bronze Process | The Ceramic Process
- The Finish | In
The Artist's Studio
|
The Very
Beginning:
- Delinda's first step in creating a sculpture
(whether in glass, bronze, or ceramic) is taken by sculpting
in clay
- or wax to create an original work. The
original is usually damaged or destroyed in the next steps: the
mold-making process.
Photo #1 Right: "Transparent" (front view),
from the Being Series of Delinda's works, in its first stage,
a clay sculpture.
Photo #2 Right: "Transparent" (side view).
Photo #3 Right: "Transparent" (back view).
Top
Of Page |
|
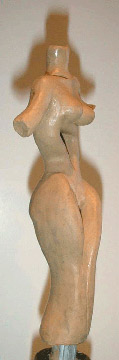 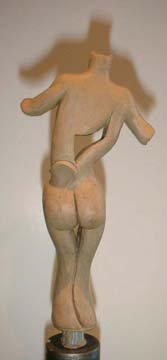
|
The First Mold-Making Process
- (for Glass, Bronze or Ceramic):
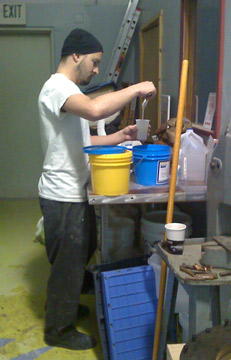 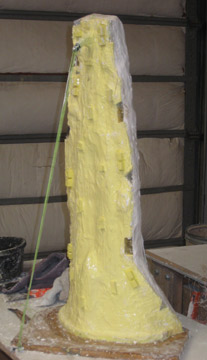
|
|
Once completed, the original is taken
to Delinda's mold-making studio where: 1) She creates a rubber
mold. The rubber mold can be a complex process, sometimes taking
several pieces to complete the whole, 2) A "mother"
mold is created to encapsulate the rubber, giving it support,
3) Hot wax is poured into the rubber/mother mold combo, creating
a wax copy of the original, 4) The wax copy is cleaned and burnished
to become the template for making the refractory mold into which
either the bronze or the glass is cast or a mold into which the
ceramic is poured or pressed.
-
- Photo #1 Left: Isaac Chavez, Delinda's studio apprentice,
is mixing a batch of silicone rubber to be used on an original
in the rubber mold-making process.
-
- Photo #2 Left: A rubber mold in process. This particular
original will be later cast in bronze to become a part of a bronze
and kiln-cast glass sculpture.
-
-
- Top
Of Page
|
The Kiln-Formed Glass Process:
- Delinda takes the wax copy, sprues and
vents it, and makes a mold (refractory mold) over the wax that
can withstand the heat of the glass process, but is soft enough
to remove without breaking the glass after it is cooled and rigid.
Some molds are more complex and require 2 or more parts, venting,
and/or reservoirs. Once the mold material is carefully mixed,
poured or applied in layers, and hardened, the wax is steamed
out of the mold, leaving a hollow negative space which the glass
will fill once fired in the kiln. The mold is either air-dried
for several months or force-dried in a kiln before the glass
is added and fired.
-
- When the mold is ready for the glass,
numerous techniques may be applied in order to fill the mold:
1) pate de verre (a paste of glass) can be carefully packed in
layers along the walls of the mold, 2) chunks of glass of different
sizes may be strategically placed into the mold, 3) sheets, slabs
or large chunks of glass can be suspended in a reservoir above
the mold, or 4) the glass can be heated in a second kiln and
poured in its flowing state into the mold. Delinda employees
all of these techniques, depending on the sculpture and the effects
she wants to achieve.
-
- After the mold is packed and ready to
be fired, it is carefully placed into the kiln for firing. The
entire firing process can take up to two or three weeks to complete
(depending on the thickness of the casting) and involves several
imperative steps to create a successful glass casting: 1) the
mold is slowly heated and held at a specific temperature to burn
off certain elements within the mold, 2) it is strategically
taken up through higher and higher temperatures so the glass
will flow properly into the mold, 3) it is continually raised
until temperatures between 1400 and 1550 degrees Fahrenheit are
reached, where the glass fully flows into the mold, 4) the kiln
is very slowly cooled and held at specific temperatures on its
way down to allow for flux and annealing of the glass, 5) when
completely cooled to room temperature, the molded glass is finally
safe to be removed from the kiln.
-
- The glass is then divested (the mold
material is carefully removed). The cast glass is then cold-worked
to achieve the artist's desired finish. Finally, the glass is
prepared for mounting.
- Delinda further incorporates kiln-formed
elements into some of her sculptures which are made by fusing
smaller sheets of glass or frit to which Delinda has applied
various techniques: painting, gold leaf, metal inclusion, enamel,
mica, irrids, etc.
|
|
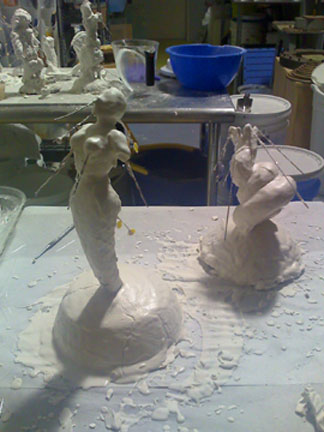
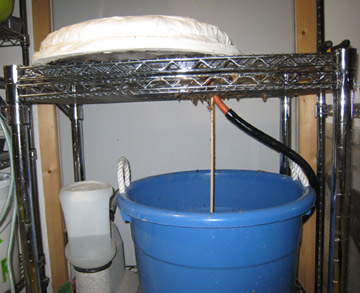
Photo Above: Refractory molds being made by applying
the refractory material in a layering process.
Photo Below: The wax is being steamed out of a
refractory mold at Delinda's mold-making studio, adjacent the
"Artifex Gallery" in Taos.
Top Of Page
|
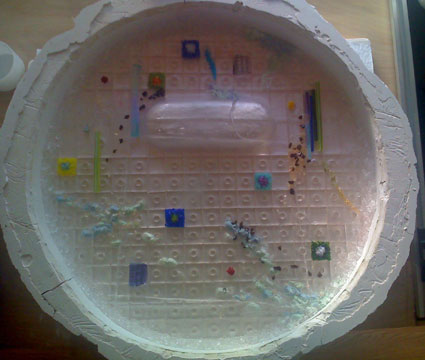 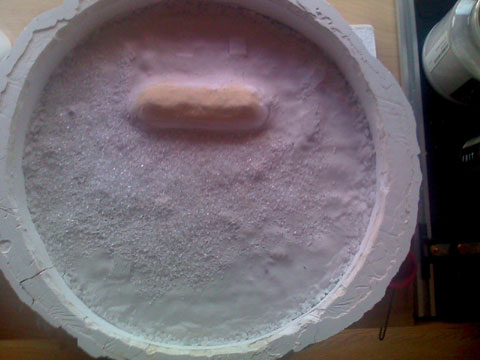 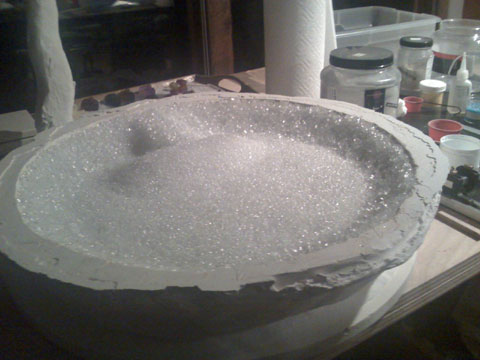
Three different stages of filling an
open face mold utilizing a pate de verre technique.
Top
Of Page |
The Bronze Process:
Once the wax copy is completed, Delinda
takes the wax to the foundry where it is prepared with sprues,
a refractory mold is made, the wax is burned out of the mold,
and the molten bronze is poured into the mold. The foundry divests
the cast bronze from the mold. Delinda receives the bronze from
the foundry and takes it back to her studio for finishing. The
bronze is "chased" (de-sprued, sanded, and blasted),
finished to fit exactly to the glass, drilled and threaded for
mounting, a patina is applied, and the sculpture is then assembled
and mounted.
Top Of Page |
|
The Ceramic Process:
Once the ceramic copy is removed from
the mold, it is re-finished and then air-dried to become leather
ware. The leather ware is placed into a ceramic kiln and fired
to the temperature appropriate for the type of clay utilized
to become green ware. The green ware is removed from the kiln
and a series of glazes are applied and re-fired to achieve the
final color and finish of the piece. The work is removed from
the kiln and prepared for assemblage with the glass elements
of the sculpture.
Top
Of Page |
The Finish:
Some of Delinda's work is entirely glass,
but she loves the challenge of combining the glass with bronze,
ceramics, or even silver, steel, paint and fiber to achieve a
particular desired artistic statement and effect.
Top
Of Page |
In
The Artist's Studio:
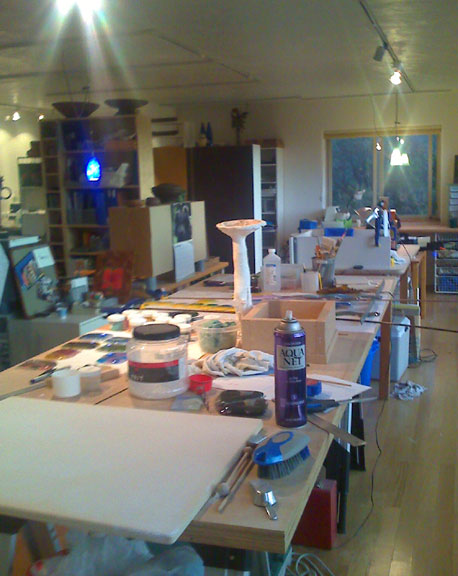 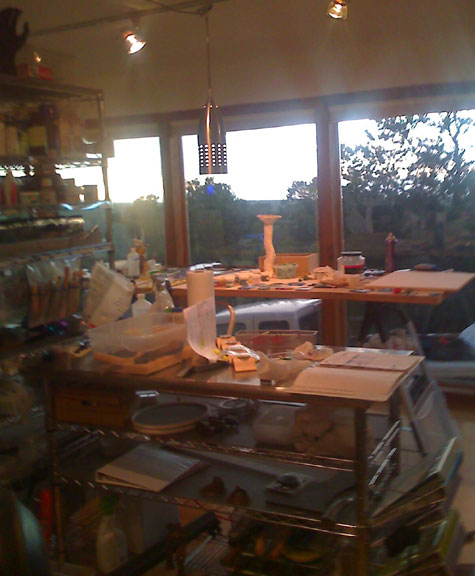 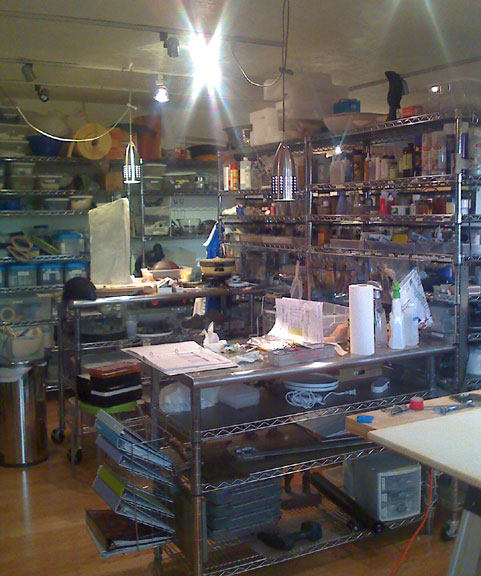
Top Of Page
|